100年余前から息づくメガネづくりへのこだわり
産地のメガネづくりの歴史は、今から113年前までさかのぼる。明治38(1905)年、増永五左衛門と弟の幸八は雪深いこの地域で、農閑期にも収入を得る手段としてメガネづくりに目をつけ、大阪から職人を招き、村の男たちにメガネづくりの技術を習得させました。二人の兄弟の思いから始まった福井のメガネ産業は現在の福井市から鯖江市にまたがる地域にひろがり、鯖江はメガネの一大産地へと成長していったのです。
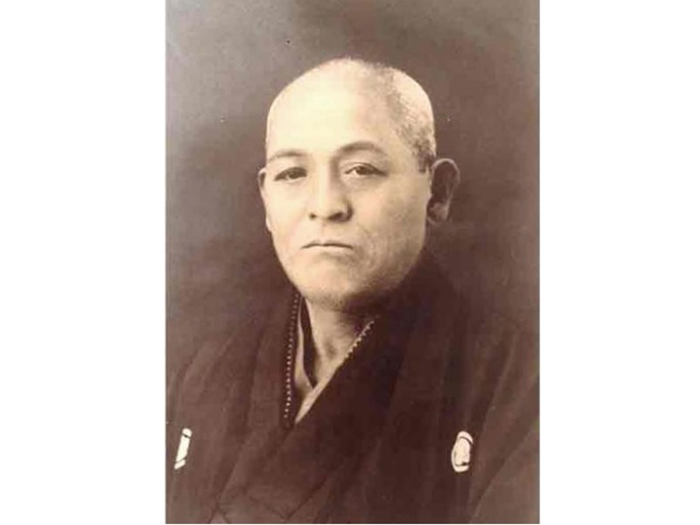
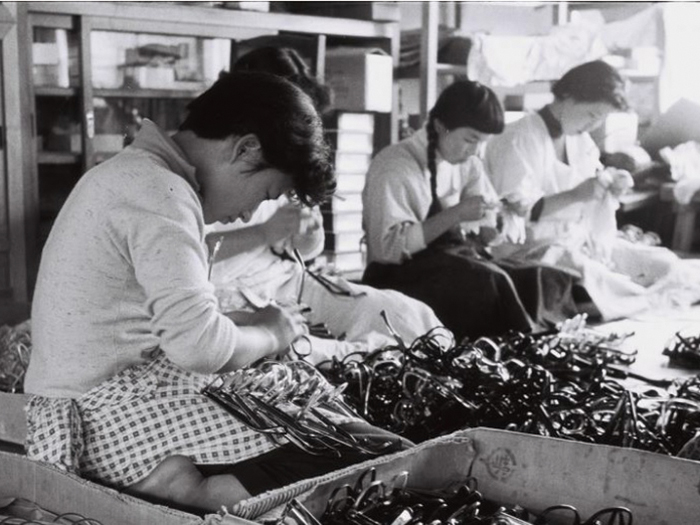
鯖江のメガネが世界から注目を集めるきっかけとなったのが、世界初の軽量素材・チタンを使ったメガネの開発です(1983年)。牧野市長いわく「先進性を受け入れる土壌がある」という産地の職人たちが地道に技術向上に取り組んで生み出した新素材のメガネは、世界的ヒットを生み、国際的なメガネの産地として確固たる地位を得たのです。
現在、「Made in SABAE」ブランドは世界的にも高く評価されていますが、その鯖江クオリティを支えているのは100年余の歴史を紡いできた職人たちのものづくりへのこだわりと、高度な技術の賜物なのです。
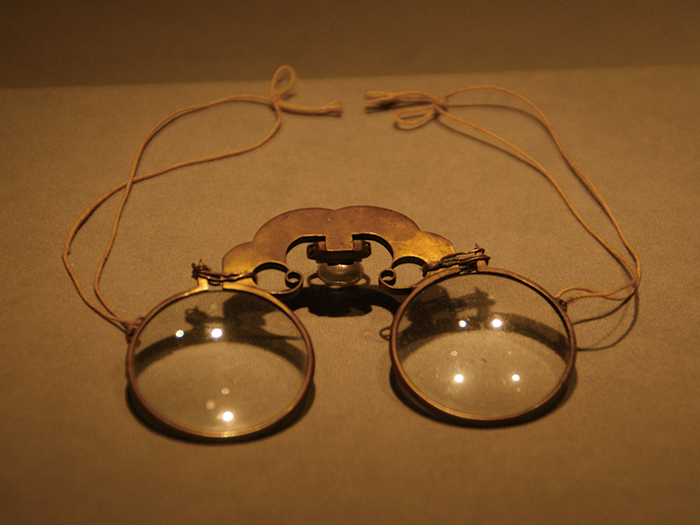
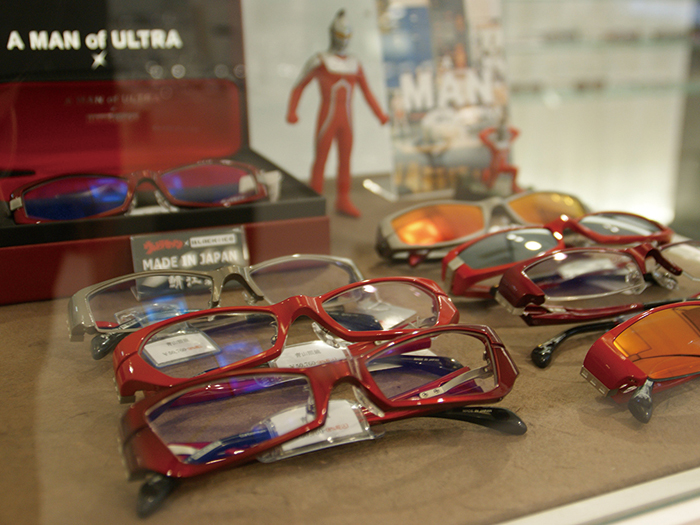
職人たちの細かな心づかいから生まれた鯖江ブランド
産地のメガネは、多いもので200以上の工程を経て完成し、それらの工程はすべて人の手が加わります。例えばメガネのテンプルをレーザーで切断するのに、図面上のデータ(数字)だけでは正しい形に切断できないこともあります。正しい形を経験値で予測し、職人自らデータを修正していくのです。デザイナーの思いを形にし、「最高の一本」をつくるために一つひとつの工程で妥協は一切しません。
●レーザー加工
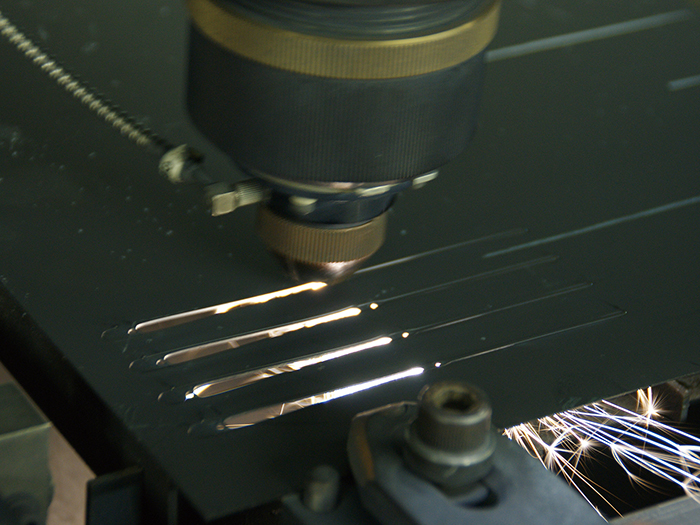
決定したフレームデザインの図面データをもとに、金属をテンプルなどのパーツに成型するための金型を作成します。図面データのままでは正しい金型ができない場合もあり、修正値を予測しながらデータの調整をその都度行います。デザイナーとの連携が重要な工程です。
●プレス加工
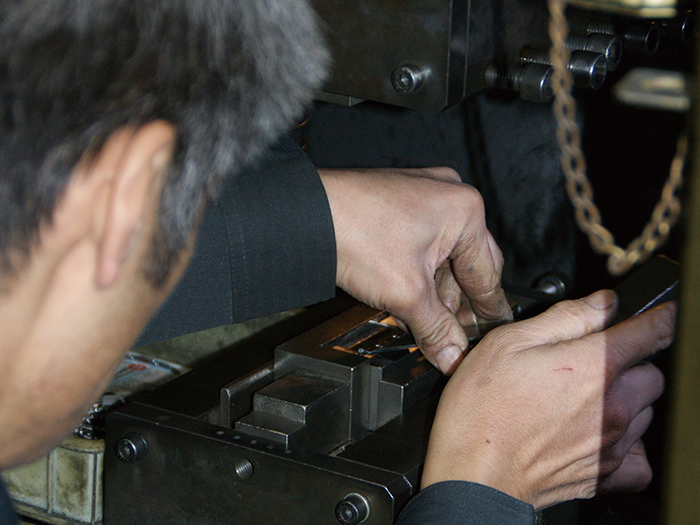
メタルフレームで使われる部品は、金型を取り付けたプレス機によって加工されます。ブリッジ、テンプル、ヨロイといったメガネフレームの核となる部品をプレスするため、この段階で良い物ができていないと、メガネの品質に大きく影響します。
動画を見る→
●メッキ塗装
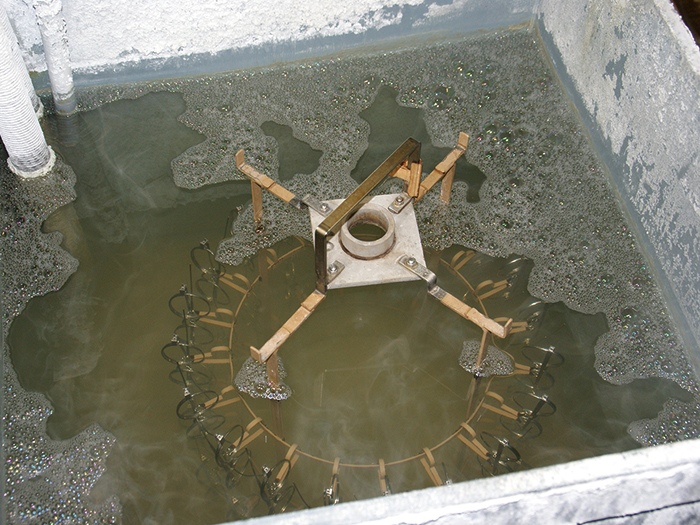
素材の腐食を防ぐ表面処理とフレームの装飾を行います。表面処理工程は10以上ありますが、見た目にはほとんど変化がない工程もあります。メタルフレームに施された金メッキは、何度も繰り返し行われた表面処理加工があってこそ美しい輝きを放ちます。
動画を見る→
似た製品はあっても「鯖江クオリティは真似できない」
産地のメガネに似た商品はたくさん存在します。ある職人はこう語ります。
「見た目は似ていても品質が違う」
細かな模様を竹串で丁寧に色づけする塗装職人、ルーペを目に当て細かい部品の調整を繰り返し行うプレス職人、「壊れないメガネ」をお客さまの元に届けるために調整・検査を繰りかえす検査職人。多くの目、手、そして経験値から生まれる鯖江メガネの品質は簡単には真似できないのです。
●組み立て/磨き/仕上げ

完成した部品を手で組み立てる作業は、キズをつけないよう、神経を使う仕事です。組み立てが完了したら「磨き」の工程へ。フレームの輝きと艶出しには熟練の技が必要です。「仕上げ」の工程ではネジのゆるみ、ねじれなどを検査。かけ心地の良さを左右するとても重要な工程です。
●印刷加工
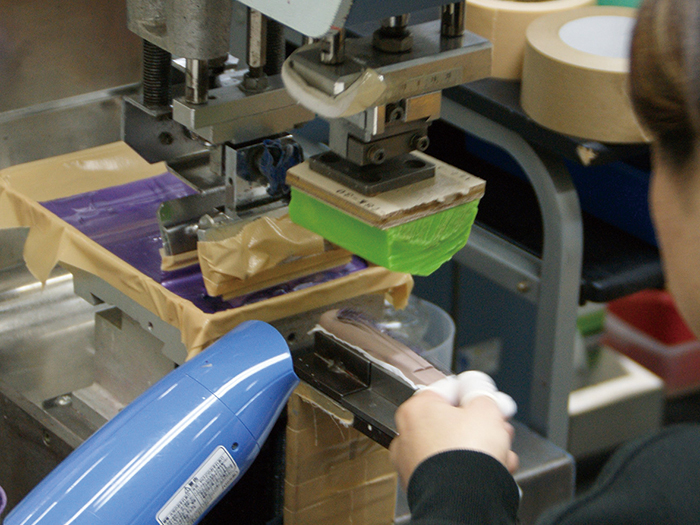
インクジェットプリントやパット印刷などが一般的ですが、3Dプリントの導入で完成イメージを動画で確認できるようになり、複雑なデザインや色のパターンサンプルをつくれるようになりました。鯖江の印刷技術は日々進化し、個性的なデザインのメガネフレームが次々誕生しています。
●修理
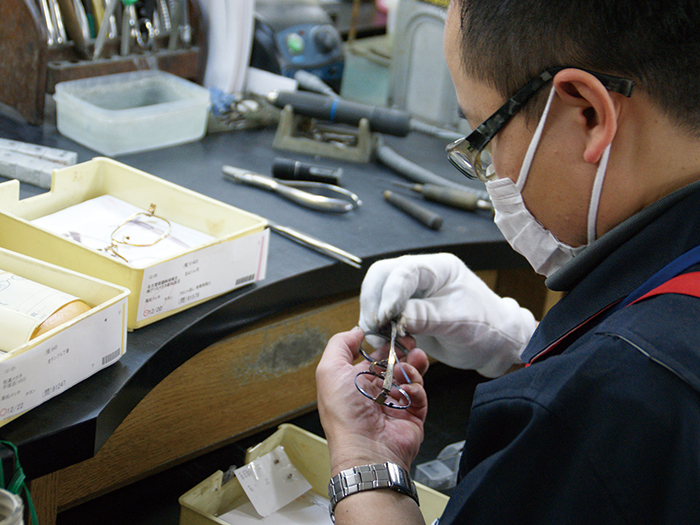
鯖江のメガネ修理工場が、国内のメガネ修理のほとんどを請け負っていると言っても過言ではありません。鯖江の職人がつくったメガネを、鯖江の修理職人たちが復元する。「つくって終わりではなく、使い続けてもらいたい」という思いがメガネの町・鯖江のものづくりの精神に息づいています。